Understanding Etchant for Stainless Steel 304: A Guide for Metal Fabricators
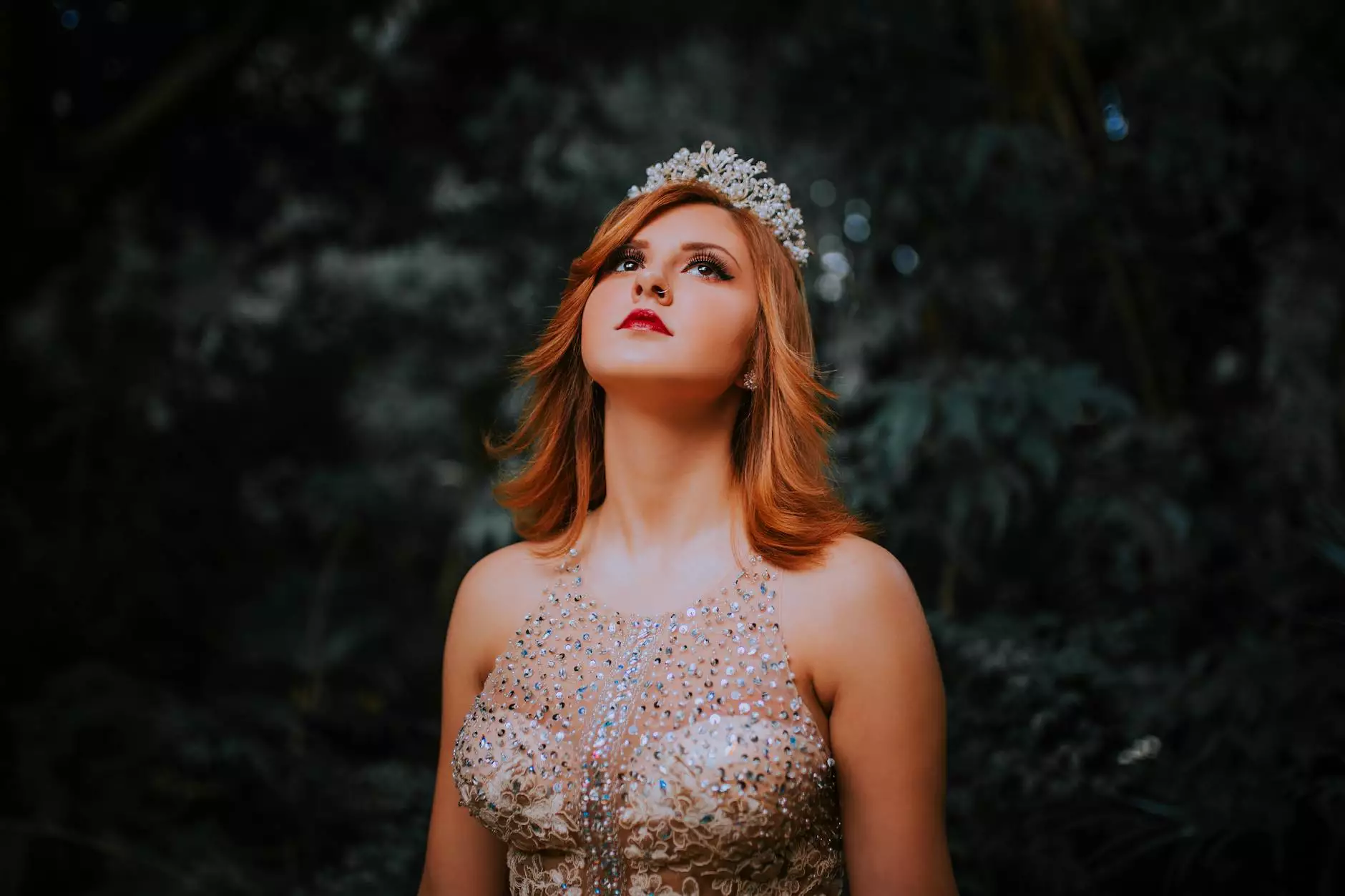
In the world of metal fabrication, precision and durability are paramount. Among the various materials frequently used, Stainless Steel 304 stands out due to its excellent corrosion resistance and versatility. However, to fully harness the benefits of this remarkable material, knowing how to effectively treat it with an etchant for stainless steel 304 is essential. This article delves into the world of etchants, providing valuable insights into their applications, types, and best practices aimed at metal fabricators.
What is Stainless Steel 304?
Stainless Steel 304 is an austenitic steel alloy that comprises 18% chromium and 8% nickel, which contributes to its notable corrosion resistance and durability. It is widely utilized across various industries, including construction, automotive, and food processing, due to its:
- High tensile strength: Capable of withstanding high stress and pressure.
- Corrosion resistance: Excellent performance in acidic and alkaline environments.
- Formability: Easily shaped into different forms, making it versatile for various applications.
- Hygienic properties: Non-porous surface that is easy to clean and maintain in sterile environments.
The Role of Etchants in Metal Fabrication
Etching is an essential process in metal fabrication, allowing for the alteration of a metal surface to achieve specific characteristics. The reasons to use an etchant for stainless steel 304 include:
- Surface preparation: Etching removes contaminants and prepares the surface for further processing.
- Enhancing adhesion: Creating micro-pores for better adhesion of coatings and paints.
- Designing intricate patterns: Used in applications such as engraving and decorative purposes.
- Removing oxides: Essential for cleaning the surface after welding or other thermal processes.
Types of Etchants for Stainless Steel 304
Different etchants are formulated specifically for stainless steel applications. Here are some of the most commonly used etchants:
1. Acid-Based Etchants
Acid-based etchants, such as hydrochloric acid, are widely used for their effectiveness in cleaning and preparing surfaces. These etchants work by dissolving the oxide layer and surface contaminants.
2. Alkaline Etchants
Alkaline etchants, typically containing sodium hydroxide or potassium hydroxide, are used for decontaminating and etching stainless steel surfaces. They are particularly useful for removing heavy oxide scales.
3. Ferric Chloride
Ferric chloride is another popular etchant known for its ability to etch ferrous materials and can be used effectively on stainless steel. This type is favored for its stability and safer handling properties compared to some stronger acids.
The Benefits of Using an Etchant for Stainless Steel 304
Utilizing an etchant for stainless steel 304 provides several notable advantages, crucial for various applications in metal fabrication:
- Improved Surface Quality: Etching refines the surface, enhancing the final finish crucial for aesthetic applications.
- Increased Adhesion: Provides a better surface for bonding with adhesives or coatings, leading to longer-lasting finishes.
- Cost-Effectiveness: Proper surface preparation minimizes wastage and enhances the durability of coatings, reducing maintenance costs over time.
- Enhanced Corrosion Resistance: By removing oxidation, etching maintains the integrity of the stainless steel, ensuring longevity.
Best Practices for Using Etchants on Stainless Steel 304
To maximize the effectiveness of etchants in processing stainless steel 304, consider the following best practices:
1. Safety First
Always wear appropriate personal protective equipment (PPE) such as gloves, goggles, and aprons. Ensure proper ventilation in the work environment to minimize inhalation of harmful fumes.
2. Pre-cleaning the Surface
Before applying the etchant, thoroughly clean the surface of the stainless steel 304 to remove any oils, dust, or other contaminants. A clean surface allows the etchant to work more efficiently.
3. Monitoring Reaction Times
Each etchant has a specified reaction time; it’s crucial to monitor this to avoid over-etching, which can result in surface damage. Test small areas first to gauge the etching time required.
4. Neutralization and Rinsing
After etching, neutralize the surface with a suitable solution to stop the chemical reaction. Rinse thoroughly with water to remove all residues, ensuring a clean surface for any further processing.
Application Areas for Etched Stainless Steel 304
The versatility of etched stainless steel 304 extends across various industries and applications:
- Architectural Details: In architectural design, etched stainless steel can be used for decorative panels, railings, and exterior facades.
- Automotive Components: In the automotive sector, etching provides enhanced design options and improves the performance of critical components.
- Food Processing Equipment: Etched surfaces are easier to clean and thus crucial for meeting hygiene standards in food preparation areas.
- Medical Devices: The precision and cleanliness provided by etching are vital in manufacturing tools and devices used in medical fields.
Common Challenges and Solutions in Etching Stainless Steel 304
While etching can significantly enhance the quality of stainless steel 304 surfaces, it’s not without its challenges:
1. Uneven Etching
This occurs when the etchant is not uniformly applied. To resolve this, ensure a consistent and even application technique, and consider using spray methods for larger areas.
2. Environmental Considerations
Etching processes can produce hazardous waste. Acknowledge and manage waste disposal according to local regulations, opting for eco-friendly etchants when possible.
3. Maintaining Quality Control
Quality checks throughout the etching process are essential. Regularly inspect and test the etched surfaces to ensure they meet the required standards.
The Future of Etching Technology in Metal Fabrication
As technology continues to advance, so do the methods employed in metal fabrication. The future of etching technology for stainless steel 304 may involve:
- Nanotechnology: Potentially introducing more precise etching capabilities at the microscopic level.
- Laser Etching: Offering speed, accuracy, and the ability to produce intricate designs without the use of chemicals.
- Environmentally Friendly Solutions: Development of sustainable etching solutions to minimize environmental impact.
Conclusion
In conclusion, the effective use of an etchant for stainless steel 304 is fundamental for achieving superior results in metal fabrication. By implementing best practices, understanding the various types of etchants, and keeping abreast of new technologies, metal fabricators can significantly enhance the quality and durability of their products. As industries evolve, staying informed about the latest trends and techniques is essential for maintaining a competitive edge.
Whether you're in the automotive industry, architectural design, or manufacturing medical devices, mastering the etching process for stainless steel 304 will empower your business to excel. Explore further with resources on goldecosteel.com for comprehensive solutions and expert insights in metal fabrication.